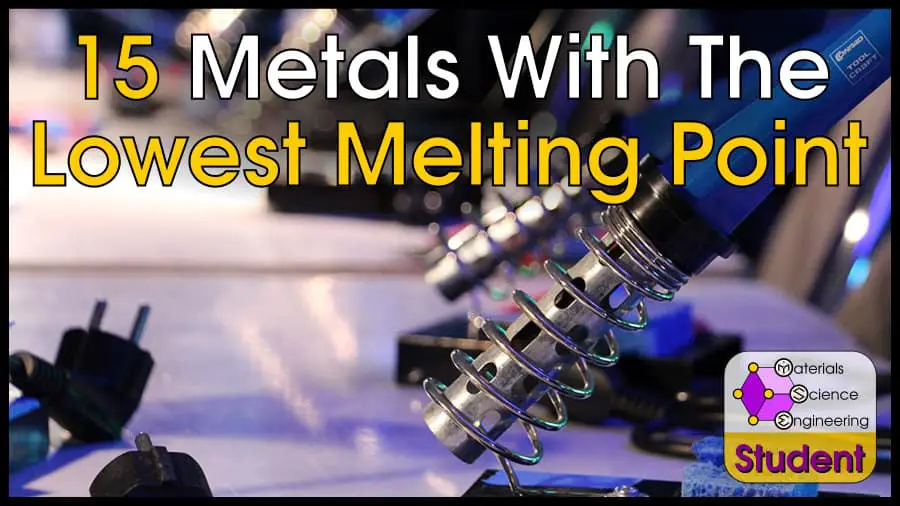
A lot of times people assume that metals have high melting points. But did you know that metals make up half of all elements that are liquid at room temperature? (There’s only 2!)
Metals can have a wide range of melting points, and you may be surprised to learn all the ways that low melting points are useful.
The melting point of a material is primarily related to bond strength. Materials with weaker bonds between atoms will have a low melting temperature. However, other factors–such as crystal structure, atomic weight, and electron structure–can also influence the melting point.
Here are 15 metals with the lowest melting points; keep reading and you’ll see all the ways these metals are useful!
15 lowest melting point metals: Mercury, Francium, Cesium, Gallium, Rubidium, Potassium, Sodium, Indium, Lithium, Tin, Polonium, Bismuth, Thallium, Cadmium, and Lead.
We also created a list of metals with the highest melting point. Check out this article to find out more!
Metal | Melting Point (oC) | Melting Point (oF) | Crystal Structure |
Mercury (Hg) | -39 | -38 | Rhombohedral* |
Francium** (Fr) | 27 | 81 | Unknown, BCC*** |
Cesium (Cs) | 28 | 82 | Body-Centered Cubic |
Gallium (Ga) | 30 | 86 | Orthorhombic |
Rubidium (Rb) | 40 | 104 | Body-Centered Cubic |
Potassium (K) | 63 | 145 | Body-Centered Cubic |
Sodium (Na) | 98 | 208 | Body-Centered Cubic |
Indium (In) | 157 | 315 | Body-Centered Tetragonal |
Lithium (Li) | 180 | 356 | Body-Centered Cubic |
Tin (Sn) | 232 | 450 | Diamond Tetragonal |
Polonium** (Po) | 254 | 489 | Simple Cubic |
Bismuth (Bi) | 271 | 520 | Rhombohedral |
Thallium (Tl) | 304 | 579 | Hexagonal Close-Packed |
Cadmium (Cd) | 321 | 610 | Hexagonal Close-Packed |
Lead (Pb) | 327 | 621 | Face-Centered Cubic |
Outline
What Makes Some Metals Have A Low Melting Point?
The simple answer is: low bond energy.
A solid can be visualized as a group of atoms bonded together that vibrate back and forth, but generally stay in the same position.
The vibration of the atoms–their kinetic energy–is what we normally call “temperature.” Higher temperature means that the atoms vibrate faster. At some point, they vibrate so quickly that they can break their bonds and slide past each other.
Each atom has a different vibration, so even in the solid state there are some atoms which are able to temporarily break their bonds and move through the material. This phenomenon is called “diffusion.”
“Melting” is when most of the bonds break. In crystalline solids like metals, all the bonds are the same length–and strength–so there is a precise point where almost all the atoms gain enough thermal energy to break their bonds. The more energy it takes to reach that point, the higher the melting point.
So when do the atoms reach this point?
Obviously, the most obvious factor is the direct bond strength. Here is a graph of bond strength (represented by enthalpy of formation) compared to melting point.
Now, there are a few more properties that influence the melting point, but wouldn’t be considered in the enthalpy of formation or bond dissociation energy. For example: how many bonds surround the atom?
In general, we consider that most effects from bonds are the result of an atom’s nearest neighbors, or the ones directly “touching” it. (Although there is an effect from atoms nearby as well–for example, if you make nanoparticles with only a few atoms altogether, the bonds are fewer than usual and the nanoparticle will have a lower melting point than the bulk material).
An element’s crystal structure determines the bond length and number of nearest neighbors (also called “coordination number”). This influences the bond strength in a way that is not captured by bond dissociation energy, but is reflected in melting point.
That’s why elements with high melting points tend to have crystal structures with high packing: FCC, HCP, or BCC. On the other hand, elements with low melting points tend to have crystal structures with lower packing.
Of course, there are still low-melting point metals with FCC, HCP, or BCC crystal structures, because these are the most stable structures.
Low Melting Point Alloys
Although there are no alloys with exceptionally high melting points, because alloying results in a lower melting point than either individual element, there are many useful alloys with low melting points, such as solders, fusible alloys, and amalgams.
When combining two elements, one extremely common point is called the eutectic point. The eutectic point has a few neat properties but the important thing is that it has a low melting point.
Here’s a graph of the melting point for an alloy of lead and tin: you can see that the lowest melting point is at around 75% tin and 25% lead. This is the eutectic point for the lead-tin binary alloy.
Of course, you can have an alloy with more than 2 base elements. Depending on the alloy system, it’s possible to have multiple eutectic points (this is hard to visualize though, since you would need more than 2 dimensions to draw it).
Fusible alloys are alloys intentionally designed to have a low melting point. They are usually composed primarily of Bi, Pb, and Sn.
Low Melting Alloy Name | Bi | Pb | Sn | Cd | In | Ga | Melting Point |
Cerrobend | 50% | 26.7% | 13.3% | 10% | – | – | 70 oC |
Cerrolow 117 | 44.7% | 22.6% | 8.3% | 5.3% | 19.1% | – | 47 oC |
Cerrolow 174 | 57% | – | 17% | – | 26% | – | 79 oC |
Field’s | 32% | – | 17% | – | 51% | – | 62 oC |
Galinstan | – | – | 10% | – | 21.5% | 68.5% | -19 oC |
Harper’s | 44% | 25% | 25% | 6% | – | – | 75 oC |
Lichtenberg’s | 50% | 30% | 20% | – | – | – | 92 oC |
Lipowitz’s | 50% | 27% | 13% | 10% | – | – | 80 oC |
Newton’s | 50% | 20% | 30% | – | – | – | 96 oC |
Rose’s | 50% | 25% | 25% | – | – | – | 98 oC |
Wood’s | 50% | 25% | 12.5% | 12.5% | – | – | 71 oC |
Solders may be considered a subset of fusible alloys. I’ll expand on his more in the applications subsection, but solders are used to join materials together–a bit like delicate welding. Historically solders have been lead-based, but as scientists have discovered that lead is a health hazard, lead-free solders (usually using bismuth, indium, and/or tin) have largely replaced lead-based solders.
Amalgams are another toxic type of low-melting point alloy. Amalgams are (were) mercury-based alloys that were used in dentistry. They are rare now, although some mercury-based alloys are used in chemical processes.
Desired Properties of Low Melting Point Materials?
Of course, metals with low melting points can be used like other metals in situations where the melting point doesn’t matter, so the regular properties like strength, ductility, electrical conductivity, etc. are useful depending on the application.
But if you’re choosing a metal specifically because it has a low melting temperature, there might be a few related properties that you also want:
Enthalpy of Fusion
This is the energy required to transform from solid to liquid at the melting point. A high enthalpy of fusion can be good because it makes the material less likely to melt if the temperature spikes too close to its melting point. On the other hand, a low enthalpy of fusion can be good because it means that it’s cheaper to melt during processing.
Volume Change
Usually, you want a low volume contraction when solidifying from liquid. High volume changes are bad because it means that the casting will have voids from the volume change. Bismuth and Gallium are unique because they expand when solidifying. These can be great for creating tight joints because the metal will expand and compress the joint when it cools.
Thermal Conductivity
Usually, you would want high thermal conductivity. Thermal conductivity tells you how quickly heat travels from one part of the metal to another–it also affects cooling. If you are using an alloy specifically because you will melt it over and over, high thermal conductivity will allow the melting to happen faster, with less heat wasted on their air or crucible. Additionally, metals used in the liquid state (like liquid tin for glass processing) should usually have high conductivity to interact with the other parts of the process.
Cycle Stability
Cycle stability refers to how much the material changes per cycle of solid → liquid → solid. During this cycle, grain size could change, composition could become less homogenous (for example, an alloy of a heavy metal and a light metal could separate so the bottom becomes denser than the top), the metal could vaporize if the boiling temperature is too close the melting temperature, the metal could react with oxygen or wet the crucible, etc. All of these things reduce cycling stability because the final product is not the same as the initial product after a heating-cooling cycle. Cycle stability is always good, but especially in applications where the metal is used in liquid form (such as tin pools for glass).
Heat Capacity
If you want an alloy specifically because it’s cheap to process, usually you want a low heat capacity. Heat capacity is how much the material’s temperature changes per input of energy–low heat capacities can reach their melting point with a low energy investment. If you are using this metal for reasons unrelated to its melting point, a high heat capacity would be good because it would make the material less likely to melt accidentally.
Toxicity
Obviously toxicity is a bad thing, and it’s a major downside of mercury and lead. In controlled environments (accompanied by lots of paperwork), toxic elements can be used in processing. In general, however, it’s now rare to put toxic elements in final products, even if there’s not much danger to the public. People still prefer to avoid lead bullets, despite the fact that lead poisoning is the least of your worries if a child is playing with a bullet.
Wettability
Wetting depends on both the liquid and the solid. Wetting refers to the angle that a drop of liquid makes with a solid, and is related to how much the liquid sticks to the solid. If you’re using metal in liquid form a lot, low wettability is usually good because it ensures that you don’t lose metal that sticks to something else.
For example, liquid tin is used to create flat panes of glass because tin does not wet glass. However, if you were using a low melting point alloy to join things (such as with solder) high wettability is a very important trait.
Diffusivity
Diffusivity is usually a concern with high melting point metals, because low diffusivity is important for creep resistance. If you are using a low melting point alloy for creep resistance, you have bigger problems to worry about. (Actually, fun fact: the reason your computer/phone gets slower over time is because the very small wires are creeping due to the computer’s heat. So for these solders, low diffusivity is preferable.) However, there are some situations where high diffusivity is a good thing. High diffusivity ensures that a liquid alloy is compositionally homogeneous. It can also be a good thing when binding materials in applications like 3D printing.
Corrosion and Oxidation Resistance
Oxidation resistance is how likely something is to react to oxygen. Corrosion resistance is how likely the material is to react with something else in the environment. In the liquid state, diffusion happens much more quickly, so reactions are especially volatile. Many metals like titanium oxidize heavily in the liquid state, so they are often melted under a vacuum. Melting in vacuum is expensive, so if you’re using pewter because it’s cheap to melt, you probably also want to be sure it doesn’t oxidize too much. The same is true for corrosion, although it’s easier to control most corrosive contaminants in a processing environment.
Flammability
Yes, some metals do burn. Magnesium is a famous example. Flammability is strictly a negative when processing. Like heavily oxidizing materials, flammable metals would require a vacuum or non-oxygen environment when processing.
Radioactivity
Yes, many several low-melting point metals are also radioactive (it turns out that unstable intra-atomic forces can also lead to unstable inter-atomic forces). Some radioactive elements are expressly used for their radioactive potential (and melting point is irrelevant), but otherwise radioactivity is a health hazard for humans.
Common Applications of Low Melting Point Metals
Metals with a low melting point can be valuable for many reasons: they are cheap to process (since a large expense in processing is usually heat), they can be used to melt and join objects together (solders), they can be used as a temperature safety valve (if the fuse gets to hot and melts, it will shut down the machine), they usually have high diffusion which can make them ideal for binding in 3D printing, and they are useful for applications that require liquid metal, since they require less energy to become liquid.
Solders are the most common use for low melting point alloys, and you could consider solders to be a subset of fusible alloys. Solders are used specifically to join objects together–similar to a hot glue gun. Solders are used in jewelry (because the metal looks the same) and in circuit boards (to preserve conductivity). Solders may also be used in a machine shop to temporarily “glue” an otherwise-difficult-to handle piece into place while working on it. Nowadays, solders are usually made of bismuth, indium, and tin, but lead used to be the main component in solders.
Safety Devices are another common use for low melting alloys. Devices such as fire sprinklers, boilers, and heated pressure vessels may have a plug made of a fusible alloy. This plug will melt at a certain temperature, relieving dangerous pressures or triggering a sprinkler system even in the absence of power. These safety plugs are very reliable because they won’t be affected by a power outage or mechanical failure, but they are also one-time use. (Well, hopefully they’ll be zero-time use). Safety devices are usually made of gallium and indium.
Bonding is a use for low melting alloys that relies on good wetting. If the metal can be liquified at a low temperature while the other parts are still solid, the metal will bond the other parts together when cool. Bonding is similar to soldering, but the term “bonding” is usually used when you consider bonding over a large surface area, while solders are usually shaped as a wire and melted at select points.
Coatings are a way to protect one material with another. For example, steel is very strong and has excellent mechanical properties, but poor corrosion properties. Although it is typical to coat steel with zinc (galvanized steel) or paint, low melting alloys made of elements like tin and gallium may also be used as a corrosion-resistant coating for structural metals.
Specific Applications of Each Low Melting Point Metal
Here is a list of low melting point metals and their applications:
Mercury
Mercury and mercury alloys (called amalgams) are useful for thermometers, and dental fillings. Mercy can also be used in mining precious metals like gold, because liquid mercury is relatively cheap and can dissolve gold.
Francium
Since francium is an extremely radioactive element, there are no commercial uses of this metal. It has been used for research purposes in chemistry and atomic structure investigations. Francium is a very rare element that decays quickly. Its half time is only 22 minutes.
Cesium
Non-radioactive cesium is commonly used in the oil & gas industry in drilling fluids. Radioisotopes of cesium are used as emitters of gamma radiation. The most interesting application of cesium is atomic clocks. They are the most accurate clocks that have been yet invented!
Gallium
Gallium is the metal with the 2nd-lowest melting point. Its melting point is low enough that it will melt in your hand (or in a cup of tea) which is the hilarious prank that names one of my favorite books, The Disappearing Spoon. A common eutectic alloy of tin, gallinstan, is made of gallium, indium and tin. This has a melting point of about -19oC, which allows it to be a liquid metal replacement for mercury in thermometers. This highly conductive liquid may also be useful as a coolant. Since gallium alloys easily with other metals and is the non-toxic metal with the lowest melting point, it is a key element in meltable safety plugs.
Rubidium
Rubidium explodes in water, so it’s not used for much in its pure state. It can give fireworks a purple color, and can also be used in experimental physics applications such as thermoelectrics, oscillators, or magnetometers.
Potassium
Potassium is a highly reactive element which significantly limits its engineering applications. It plays an important role in nutrition. Potassium oxides can be used in glass and soap manufacturing. Like all group 1 metals, it’s more used for its chemical properties than as a bulk metal.
Sodium
Sodium also explodes in water (or at least catches fire), and is much better known for its use in table salt and other chemical compounds. Sodium can be used to create yellow in fireworks, or in sodium lamps, but is not really used in pure form except as an intermediary step to some other chemical.
Indium
Indium is often alloyed with gallium for many of the same applications. Indium is also a key component in lead-free solders.
Lithium
In materials science and engineering, lithium is used in the aircraft industry. It is added to aluminum for the purpose of weight reduction. Besides lightweight Al-Li alloys, lithium is used to produce lithium-ion batteries for electronic devices. It is also used as a source of tritium for nuclear applications, and has uses in medicine.
Tin
Tin is a very useful metal, because it has a low melting point and is also nontoxic. Tin is alloyed to make pewters, although most of the world’s tin is used to make solders. Solders are pieces of metal that are melted and then used to join other objects together. Solder can be used to join jewelry together, although its most important use is in connecting wires on circuit boards. Tin is also used to make flat glass (this has been a problem since antiquity): since glass does not stick to tin and is less dense than tin, a common method of making flat window glass is to melt the glass on top of a pool of molten tin. The glass will float to the top, form a flat sheet, and can be cooled into a flat pane.
Polonium
Polonium was discovered by Pierre and Marie Curie and named after her country of birth, which means–you guessed it–it’s radioactive and extremely toxic. Polonium has some niche uses that take advantage of its radioactivity, but the metal is rarely intentionally alloyed. One example I found was a nickel-based alloy with trace amounts of polonium, designed to create intentionally radioactive spark plugs. Allegedly, these radioactive spark plugs allowed for better fuel combustion, but they would have needed frequent replacing, considering polonium’s half life.
Bismuth
Unlike most materials, bismuth expands when it solidifies (this is probably because it has a monoclinic crystal structure which has terrible packing and likely contributes to the metal’s low melting point). Bismuth’s cooling expansion makes it excellent at joining other materials since the expanded part will apply extra pressure to keep everything together. Bismuth is also a cheap, nontoxic alloying addition to solders. Since bismuth also has a high density and similar softness to lead, it is often used as a non-toxic replacement for lead, even beyond solders. (Bismuth crystals are also pretty, and can be used to draw like pencil lead).
Thallium
Possibly the liquid metal with the lowest possible melting point is the eutectic between mercury and thallium (8.5% thallium). If you’re worried about the toxic mercury in that alloy, you should actually be even more concerned about the thallium’s toxicity. Not only is thallium extremely toxic, it can also be radioactive–which is why you’ve probably never heard of this metal before now.
Cadmium
Cadmium is notably corrosion-resistant, which means that it can be used as a protective coating for metals such as steel. Cadmium can be toxic, especially if it seeps into the environment and ends up in the food chain (this is why you should recycle your batteries!). In bulk, however, the metal is not that dangerous and can alloy in solders as a safer alternative to lead.
Lead
Everyone knows lead is toxic (it’s a neurotoxin), but it has been an extremely useful metal for centuries–in part because it was easy to mine, but also because its low melting point makes it easy to cast. Lead is also soft, ductile, and relatively oxygen-resistant. Lead has been used in solder, bullets, fishing lures, batteries, pewters, fusible alloys, paints, and more; although governements and environmental agencies have been trying to reduce lead use for decades.
Final Thoughts
Many people think that high melting point alloys are more useful than low melting point alloys, but I hope you now know that’s not the case!
Low melting point metals are extremely useful for a variety of reasons, although they also have an unfortunate tendency to be toxic or radioactive. Low melting point metal elements tend to have non-close-packed crystal structures, as well as low bond energy.
By utilizing eutectic points in alloy composition, engineers have been able to reduce the melting points of certain alloys below the pure element melting point, even creating gallinstan, a nontoxic replacement for mercury that is liquid at room temperature.
References and Further Reading
If you liked this breakdown of low melting point metals, you may also be interested in my explanation of high melting point metals! In that article, I focus more on the properties that affect high melting point.
For a more technical look at low melting point alloys, here is a nice scientific review.
If you want to learn more about those radioactive Polonium spark plugs, check out this webpage.
This paper and this article are our sources of chemical compositions of low melting alloys.
If you enjoyed looking at a few applications for a variety of different elements, you will probably also enjoy Sam Kean’s The Disappearing Spoon. This might be the only book my wife and I both owned before we met each other, so now we have it in two different languages!