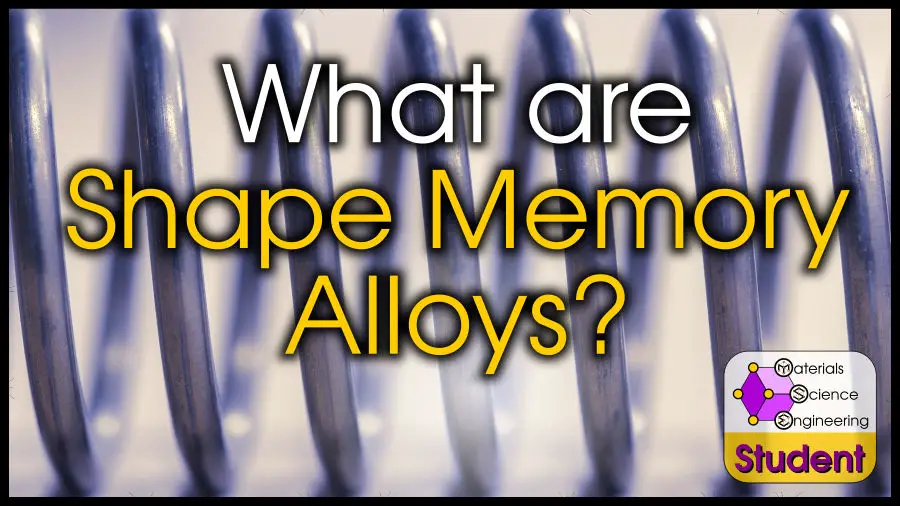
Shape Memory Alloys (SMAs) are one of the coolest things in materials science. Every couple years, I see a shape memory alloy video go viral on reddit, facebook, or your social media platform of choice. When I started college as a freshman in materials science, the first thing I did was find a research group where I could investigate shape memory alloys.
Shape Memory Alloys (SMAs) are an intermetallic alloy that can be deformed but will return to their original shape when heated. SMAs have a Shape Memory Effect (SME) and pseudoelastic effect, which are related to the same underlying mechanism.
SMAs work because deformation happens via detwinning (instead of dislocation motion) which can be undone in a martensite → austenite phase transformation. SMAs could be the key to more efficient airplanes and more accurate robot controls (including prosthetic robotic hands, like in Star Wars).
If that was a lot of vocab words, don’t worry! SMAs are my absolute favorite material, so I’m going to be very comprehensive, but I’ll walk you through this step-by-step. I’ll include some advanced metallurgy (and basic materials science concepts) in collapsable text.
Outline
Introduction to Shape Memory Alloys
Do you remember the liquid metal terminator from Terminator 2? Shape memory alloys are the closest thing we have to that.
SMAs are a class of smart material that can remember their shape. You bend them and they will return to their original shape when heated (or experience other stimuli, like a magnetic field for magnetic shape memory alloys).
Additionally, SMAs are extremely elastic (that means they can bend far and return to their original shape, like a rubber band).
SMAs have this property because of two unique intermetallic phases. We call these “austenite” and “martensite,” the same words used for steel, although these phases share nothing in common with steel.
Current shape memory alloys are:
- NiTi, or nitinol. This is the most developed SMA, with excellent mechanical properties. It is pretty much the only commercially viable SMA.
- Cu-Al-Ni, Fe-Mn-Si, and Cu-Zn-Al systems. These have poorer mechanical properties and are still in development, although they may one day offer advantages over NiTi such as higher transformation temperatures
- Ni-Mn-Ga. A magnetic shape memory alloy, which is affected by magnetic fields rather than temperature. Magnetic shape memory alloys are also in the developmental stage.
- Other alloys also exist, which are even less commercially viable. Alloys with gold, silver, platinum, and palladium have made good SMAs in the laboratory, but they will probably never be worth the cost of the raw materials.
When discussing shape memory alloys, there are a few vocabulary words you might want to know:
- Martensite. This is the low temperature phase.
- Austenite. This is the high temperature phase
- Transformation temperature. This is the temperature at which the phase changes between austenite and martensite. Actually, the temperature is a range and depends on whether you are heating or cooling, so there is a martensite start temperature (Ms), martensite finish temperature (Mf), austenite start temperature (As), and austenite finish temperature (Af).
Shape memory alloys are actually shape memory intermetallics. Alloys are combinations of metal elements that form a solid solution and maybe precipitates (the precipitate can be an intermetallic).
Intermetallics are not in solid solution, but instead have directional bonding and an exact stoichiometric relationship. You can read this article to learn all about the difference between alloys and intermetallics, but this picture is a quick summary:
SMA Phase Breakdown
The most common SMA is NiTi, also called nitinol. NiTi, in theory, has an exact ratio of 50 at.% Ni to 50at.% Ti. The austenite (high temperature) phase in NiTi is usually B2. The low temperature phase (martensite) is B19. B19 is complex and is hard to understand with a simple drawing, so here’s a thorough look at the B19 crystal structure.
B2 is an intermetallic body-centered-cubic phase. You can imagine a cube with atom A on all the corners, and atom B at the center of each cube. In this case, the two atoms would be Ni and Ti.
Technical point!
I’ve drawn B2 structure with Ti at the center of each cube and Ni at the corners, but by translational symmetry and redefining the origin, you could also imagine that Ti is at the corners and Ni is in the center. It’s just a matter of perspective.
Ti would always be at the center of each cube, and Ni would always be at the corners. In NiTi, there is some slight tolerance for error–if you had too many Ti atoms, a few Ni atoms could be replaced, and vice versa.
However, these intermetallic substitutions have a large effect on the transformation temperature.
This graph from Dr. Tom Duerig shows how the transformation temperature can change over 100 °C from just a 1% change in the Ni-Ti ratio.
Why are Shape Memory Alloys Useful?
I’ll discuss specific applications for shape memory alloys in a later section, but why would scientists be interested in these smart materials at all? (Besides the fact that they are just awesome to play with).
Since SMAs change shape when they are exposed to heat, they can do work. In principle, you could use them to convert thermal energy into mechanical energy. You could technically build a motor with a wire made of this alloy, although that’s not their most useful feature.
SMAs are most often talked about as actuators (actuators are basically small switches that move things, especially in robots).
Imagine the flaps on an airplane wing. This is one example of an actuator.
Actuators are usually made of many parts–you have gears, joints or hinges that bend, electronic sensors, a motor to push and a motor to pull, and maybe even more parts. All of these parts for the actuator represent a part that can fail, will require maintenance, and adds weight.
What if you could replace all of these parts with a single part, made of an SMA?
Doing this would reduce the complexity of the system. It would save time on maintenance and reduce the possible points of failure. It would require less material and weigh less (very important in aircraft). All you would need is a shape memory alloy and something to control its temperature. Temperature is one of the easiest energy sources for humans to control, arguably even easier than electricity.
One of the most interesting potential applications for shape memory alloys is in prosthetic, robotic hands (like in Star Wars). Currently, robot hands are not that feasible because they require a lot of maintenance, they are bulky, and they weigh too much.
Here is a servo motor prosthetic hand from Siong et. al. You can see how bulky it is.

SMA replacements may be more precise while also solving these issues, although this is in the future (those researchers only finished 1 finger in their paper).
What is the Shape Memory Effect?
At last, the magical effect that gives SMAs their name!
The shape memory effect (SME) is what allows SMAs to return to their original shape after heating. The SME is a temperature-induced martensite-to-austenite phase transformation.
That means that heat causes the alloy to change from martensite (B19) to austentite (B2). When this phase transformation happens, something causes the material to resume its original shape. What is that “something?”
To explain this, you need to understand a bit of metallurgy. Specifically, you need to understand dislocations and twins.
When a material deforms, its atoms are moving. There are 3 ways that the atoms can move:
- Bond stretching. This is what causes elastic deformation and Hooke’s law. All materials show atomic bond stretching when a force is applied.
- Dislocation motion. This is how (most) metals deform, and it’s the reason that metals are ductile. A row of atoms can slip past each other and rebond, since metallic bonding is nondirectional.
- Twinning. Twinning is caused by crystal atomic planes mirroring each other. In most metals, dislocation motion is easier than twinning, so most metals don’t twin much.
Remember how I said that NiTi was an intermetallic? That means that dislocation motion is much more difficult because each dislocation creates an antiphase boundary.
Since dislocation motion is more difficult, that leaves room for twins to occur–or more precisely, detwinning.
Suppose that your SMA starts at high temperature, in the austenite phase. It has a certain shape.
As you cool down the SMA, austenite will transform into martensite. The atoms shift slightly, but don’t move much overall. There is no shape change. But notice that there is now a zig-zag line?
This is where detwinning will occur. Now if you bend the martensitic SMA, the bends will be accommodated by detwinning, not dislocation motion. Because the deformation was detwinning, each atom is still surrounded by its same neighbors.
If you heat the SMA so it turns back into martensite, the phase change happens again. Since the relative positions of each atom have not changed, when the atoms realign into austenite, they realign exactly as they were before they were deformed.
That is why the shape memory effect happens. It is the coincidence of 2 phases that have a military-order transformation, combined with deformation mode of twinning.
It is also possible to have a two-way shape memory effect by repeated training from one phase to the other.
What is Pseudoelasticity?
Shape memory alloys are extremely flexible. I remember when one of my professors handed me a SMA tube and told me to bend it, I bent the tube about 30 °C and expressed my amazement. Another student bent the tube into a pretzel!
Most people don’t know about this effect, and those that do usually call it “superelasticity.” in my opinion, this name is incorrect. Elasticity comes from atomic bond stretching–so a superelastic material would have atomic bonds than can stretch far.
Shape memory alloys achieve their flexibility by an entirely different means. The atomic bonds don’t stretch, so it is “fake” elasticity, or “pseudoelasticity.”
SMAs display pseudoelasticity in the austenite phase, for a very similar reason as the SME in the martensite phase. The SME is a temperature-induced phase transformation, while pseudoelasticity is a strain-induced phase transformation.
Phase diagrams are functions of both pressure and temperature. Here is a pressure-temperature phase diagram for iron: you can see that phase transformations can happen by pressure or temperature.
Why are pressure-temperature phase diagrams so rare in materials science?
We usually ignore pressure because atmospheric pressure is harder to control than the temperature, and most engineering materials are not very pressure-sensitive, but strain is another kind of pressure.
More importantly, shape memory alloys have what is called “displacive” or “military-order” phase transformation. That means that the transformation happens instantly by atoms shifting, and doesn’t require thermal energy to move atoms into position. In this iron phase diagram, you probably wouldn’t see hexaferrum even at 130 kbar (which is about 130x the pressure of the atmosphere) because the atoms would need thermal energy to diffuse quickly (unless α → ε is also a military-order transformation, but there’s not much research on this because the pressures are hard to obtain).
If you have a SMA which is in the austenite phase, above the transformation temperature, applying a strain will cause the austenite to transform into martensite. You can think of it as the strain lowering the transformation temperature.
Since the SMA is now martensite, bending it causes detwinning instead of dislocation motion. Thus, the deformation is potentially reversible.
When the force bending the SMA is removed, the transformation temperature returns to normal, and the material transforms from martensite to austenite, reversing the detwinned deformation just like the SME.
Basically the shape memory effect is when you change the SMA’s temperature to be below → above the transformation point. Pseudoelasticity is when you change the transformation point to be above → below the SMA’s temperature
If you want to know more about the relationship between pseudoelasticity and the shape memory effect, click here!
Here is a graph of stress and temperature, with some important lines drawn.
You can see 4 vertical lines, corresponding to the martensite start and finish temperature, and the austenite start and finish temperature. As you heat the SMA, martensite will begin turning into austenite at As, and the sample will be fully austenitic at Af and above. When cooling the SMA, austenite will start to turn into martensite at Ms, and the sample will be fully martensitic at Mf.
Yes, that means there is hysteresis. I’ll talk about this more in my article about SMA research, but imagine you are at a temperature between Ms and As. Will the SMA be austenitic or martensitic? It depends on whether you are heating or cooling. If you are cooling, that point will be austenitic. If you are heating, it would be martensitic. Go hysteresis!
Now there is a mostly flat line: the critical stress for slip. This is the stress where the atoms slip instead of twin. (Above the line means the atoms slip, below the line means they twin). This line has a negative slope, because slip becomes easier as temperature increases.
The SME and pseudoelasticity can only be possible below this critical stress, because detwinning is necessary for both of these mechanisms. For most materials, this line for critical stress is very low and these materials slip instead of twin.
Finally, there is a line with a positive slope, which is the critical stress to induce martensite. Stress makes martensite more likely, while temperature makes austenite more likely, so the line increases with increasing temperature. Below this line, the stress is not enough to overcome the temperature, and the austenitic phase will bend normally, without a pseudoelastic effect. Above this line, there is pseudoelasticity.
Applications of Shape Memory Alloys
When I say applications of SMAs, I really mean applications of NiTi. This alloy has excellent mechanical properties, is relatively cheap and easy to make, is non-toxic and can be used for biomedical applications, has good corrosion resistance . . . and also has the SME and pseudoelasticity.
If you have ever seen a metal that was extremely flexible–that’s probably NiTi. This alloy is used in glasses frames, bra clips, and wiring for braces.
The stress-induced transformation (pseudoelasticity) also absorbs energy without moving, so SMAs can be used for vibration dampening. It would be similar to the way that a half-melted ice cube would stabilize temperature fluctuations around 0 °C, because the ice would freeze or melt slightly while still staying the same temperature.
By utilizing the shape memory effect, doctors can use them as stents to open up blood vessels and help clear clogged arteries.
SMAs can be used in safety devices like shower heads. Imagine that the hot water was accidentally too hot, and you could accidentally burn yourself (or a child). An SMA could be built into the showerhead which would instantly close off the water if the temperature was too high.
As I mentioned earlier, the most promising application of the shape memory effect is in actuators. Actuators are small parts that move, like fingers in a robotic hand or flaps on an airplane. Current actuators are usually electric motors, hydraulics, or pneumatics, which are complex (and therefore heavy). These actuators need increasing complexity for 3D motion, while SMAs can actuate equally easily in 2D or 3D.
Shape memory alloys are a single piece of material which can save weight and possibly be less likely to fail than complicated motor systems with intricate pieces that fit together. Currently SMAs are not ready to do this yet because they are limited by fatigue life, but this is a promising potential application.
Used for Pseudoelasticity
- Glasses frames
- Bra clips
- Orthodontics
- Metal plates to help bone grow together
- Vibration dampening for jets or other engines
- Structure stabilization (like for earthquakes)
Used for SME
- Temperature-sensitive safety devices
- Stents
- Actuators (especially prosthetic hands or airplane flaps)
- Motors (not really, but it’s theoretically possible)
The Future of Shape Memory Alloys
Current shape memory alloys face three main challenges: increasing fatigue lifetime, increasing the transformation temperature, and reducing cost.
There are also some SMA systems (such as CuAlNi) which have high transformation temperature, but poor mechanical properties. But I’ll focus on the NiTi system, since that is what is currently used (more for the pseudoelastic effect than shape memory effect though).
My undergraduate research focused on increasing the transformation temperature of SMAs. This can be done by alloying elements (Hf, Pd, and Pt are good candidates) or by using a non-NiTi system and trying to fix the problem with the other system.
Since the SME is triggered by increasing the temperature past the transformation point, SMAs only work if the ambient temperature is below the transformation point. In NiTi, it’s difficult to achieve As much higher than 100°C. 100°C is an important number because it means the SMA can work in water without any danger of accidentally overheating.
However, for the SME to work on high speed aircraft (which would most-benefit from reduced weight from SMA actuators), the transformation temperature would need to be in the 300°C to 400°C range to avoid accidentally triggering just because of air resistance.
One way to achieve higher-temperature SMAs (with good mechanical properties) is to substitute elements for Ni and Ti. However, the elements that raise the transformation temperature also tend to be very expensive, such as platinum, palladium, hafnium, and gold. I worked with a TiPd-family of SMAs in one of my internships, and I later realized that my (very small) samples cost around $5,000 in palladium alone.
Perhaps the weight savings on spacecraft will be worth the cost, but that is an unacceptable price for most applications on this planet.
The third main challenge facing applications of the SME is fatigue. Fatigue is when a material can do something easily once, but fails when it tried to do that same thing many times. For applications like emergency devices, fatigue is unimportant because they are designed to be used only once.
But how many times would a robot bend its fingers in a lifetime? Ten thousand times? A million times? The shape memory effect works because deformation happens by twinning instead of dislocation motion. But every time the material is deformed, there is still the possibility of dislocations moving. If one dislocation moves, the material will permanently deform by one atomic radius.
That’s not so bad–it would take perhaps 1013 dislocations for this deformation to be noticeable, but in reality, there are probably at least a million dislocations moving each time the material is deformed. If 10 million dislocations move each cycle, the part will only last for 1 million cycles. This will be fine for many applications, but in practice there may still be 100 million, 1 trillion, or more dislocations moving in each cycle (for reference, a trillion is 109 and bending a paperclip would be around 1018 dislocations moved).
There are SMAs that can survive a million cycles of SME changes, but fatigue is another limiting factor that prevents other SMAs from competing with NiTi.
The future of SMA research will improve fatigue, transformation temperature, and cost.
And once these requirements are met, lighter airplanes, robotic prosthetic hands, and more will be possible.
Another up-and-coming type of shape memory alloys are magnetic shape memory alloys. I have not worked with these before, but you can find an open-access review paper here.
How Can I Make my own Shape Memory Alloy?
Unless you have a laboratory, don’t try to make an SMA from scratch. You would need very expensive equipment to do this safely.
However, you can directly buy SMA wires and play with them all you want!
If you want to perform some of your own experiments, I found this handy SMA laboratory guide.
To create your “permanent” shape, you need to heat the alloy into the austenite region far enough that pseudoelasticity disappears. Then you can deform the wire into the permanent shape that you want.
When you cool down the sample, it will return to martensite in this shape. Now you can deform it however you want, heat it by using an air dryer or dunking in warm water, and it will return to the shape you set!
If you want to see the pseudoelastic effect, you should buy wire with an transformation temperature below room temperature. This SMA will be austenitic at room temperature. You can then bend it and watch it recover its shape, like rubber!
Final Thoughts
Shape memory alloys are awesome! They have a temperature induced transformation martensite–>austenite, which gives the shape memory effect (SME); as well as a stress-induced transformation austenite–>martensite, which give the pseudoelastic effect.
SMAs have hysteresis loops in both stress-strain space and temperature-strain space. Here is a summary image (projected from 3 dimension) which shows all of this.
Shape memory alloys are currently used for tons of applications that utilize pseudoelasticity, such as glasses frames. When scientists can improve the shape memory effect, especially fatigue life, SMAs will be the material of choice for actuators. Imagine making an entire airplane wing out of a single piece of metal!
References and Further Reading
If you liked this article about an advanced alloy system, you may also be interested in my article on superalloys! If you want to go back to the basics and dig into the difference between alloys, intermetallics, and composites; I suggest this article. You might also find this post, which is all about alloys, useful too!
I did research on shape memory alloys, so I’ve read a lot of papers. If you might be interested in studying SMA metallurgy, here are three reviews you can read without a journal subscription:
- A review of shape memory alloy research, applications and opportunities
- Shape memory alloys: a state of the art review
- NiTinol 60: A Review of Recent Research Findings, Potential for Structural and Mechanical Applications, and Areas of Continued Investigations
I didn’t talk much about magnetic SMAs, but if you’re interested in a review about them, you can find one here.
If you are very serious about shape memory alloys (maybe you started a PhD project about them and are frantically searching for all the information you can find), this article is one of the most comprehensive and advanced reviews on shape memory alloys (you need a journal subscription).
If you are interested in the paper that discusses the possibilities of making a robotic hand out of SMA actuators, here is the paper I got that image from.
And if you want some cool ideas for experiments to test with your newly bought shape memory alloys, here is a guide for teachers to design laboratory experiments with SMAs.