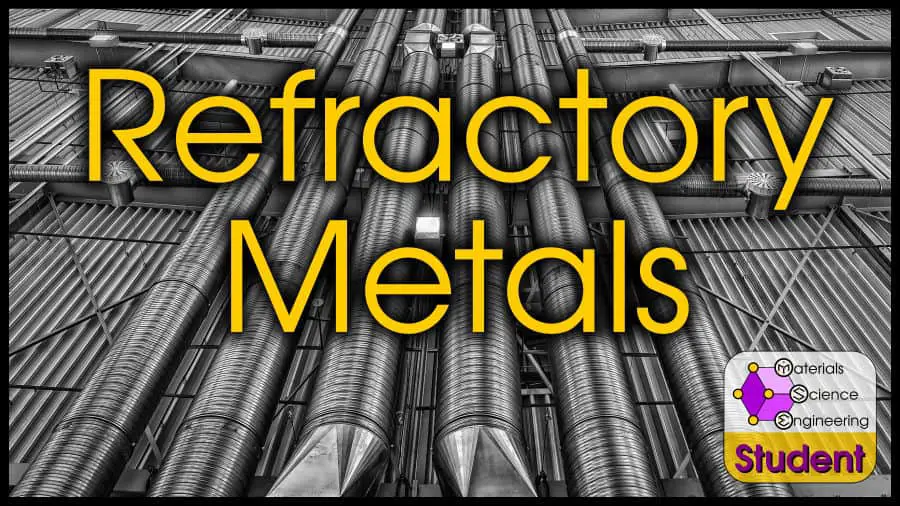
“Refractory metals” is one of those colloquial terms used to group materials with extremely high melting points. Refractory metals share several features with each other, depending on the user’s definition.
Refractory metals are the metallic elements with the highest melting point, high hardness, and high density. Conservative definitions of “refractory” refer to 5 industrially useful metals with a melting point >2000°C: tungsten (W), rhenium (Re), tantalum (Ta), molybdenum (Mo), and niobium (Nb). Broader definitions include up to 15 metals.
In this article, I will explain common applications for all 15 refractory metals.
Outline
Undisputed Refractory Metals
The 5 undisputed refractory metals are tungsten, rhenium, tantalum, molybdenum, and niobium.
- Tungsten (W) 3380°C, BCC
- Rhenium (Re) 3180°C, HCP
- Tantalum (Ta) 3014°C, BCC
- Molybdenum (Mo) 2617°C, BCC
- Niobium (Nb) 2468°C, BCC
These metals are generally dense, hard, and have a very high melting point. They are also abundant enough to be useful in general engineering applications. Osmium is an example of a metal with a high melting point that is not always considered a refractory metal–although it has the 3rd highest melting point of any metal–because it is rarely used at high temperatures (its oxide is toxic).
Broader List of Refractory Metals
In addition to the metals listed above, we might also consider all metals with a melting point >1,650°C to be refractory metals:
- Osmium (Os) 3027°C, HCP
- Iridium (Ir) 2447°C, FCC
- Ruthenium (Ru) 2250°C, HCP
- Hafnium (Hf) 2227°C, HCP
- Technetium (Tc) 2200°C, HCP (Radioactive)
- Rhodium (Rh) 1963°C, FCC
- Vanadium (V) 1902°C, BCC
- Chromium (Cr) 1857°C, BCC
- Zirconium (Zr) 1852°C, HCP
- Titanium (Ti) 1670°C, HCP
Some of these metals–such as zirconium, titanium, vanadium, and chromium–are not included in the more-strict definition because they have low density and their melting point is below 2000°C. Others are not commonly used for industrial high-temperature applications because of cost (Ru, Ir, Os), toxicity (Os), or even radioactivity (Tc).
Common Properties of Refractory Metals
All of the refractory metals have a close-packed or nearly close packed crystal structure: FCC, BCC, or HCP. Most of them have a BCC crystal structure. Of the 5 undisputed refractory metals, 4 have a BCC structure and 1 has an HCP structure.
My best explanation for the high melting points associated with a BCC crystal structure is that it is nearly close-packed so it’s generally stable, but it has more empty space than a truly close-packed lattice, which gives the atoms more room to vibrate before breaking free from the lattice. For a (very complex) mathematical proof of why BCC tends to be the most stable high-temperature phase, check out this paper by Alexander and McTague.
All refractory metals have a very high melting point. Depending on who you ask, there may be different temperature cutoffs. Niobium has the lowest melting point of traditional refractory metals, but it’s still higher than 2400°C. In the expanded list that I present, zirconium has the lowest melting point at 1850°C.
Refractory metals tend to have a high density (tungsten and osmium are the heaviest elements) and high hardness (tungsten and rhenium are known for their hardness). This combination makes refractory metals useful for applications requiring high wear resistance; however, many refractory metals are also brittle.
Refractory metals usually do not corrode easily. In fact, iridium, osmium, rhodium,and ruthenium are both refractory metals and noble metals.
However, refractory metals do oxidize easily.
Because of their combination of high strength and temperature resistance, refractory metals are relatively creep resistant. Since they often have low diffusion rates, they are especially useful for alloying with other elements to improve creep resistance of the base alloy.
Applications
Tungsten (W)
The metal that can withstand the highest temperature is not especially expensive either, so tungsten is the go-to metal for high-temperatures applications such as light bulb filaments, welding electrodes, and furnace heating elements.
Rhenium (Re)
Used in superalloys for jet engines to slow down diffusion (basically 70% of extracted rhenium is used for this purpose). It’s a rare/expensive element, so it’s rarely used as the main base metal in an alloy.
Osmium (Os)
Actually, its applications have almost nothing to do with its high melting point because osmium oxide is super toxic. However, it can be extremely hard/wear resistant at regular temperatures–for example, you may have used an alloy of osmium and iridium for fountain pen tips.
Tantalum (Ta)
Tantalum is used to make high temperature, corrosion resistant alloys, such as ones used in vacuum furnace parts.
Molybdenum (Mo)
Like many other materials on his list, molybdenum is primarily used to alloy with other metals. It sees significant use in superalloys for jet engines. It is a useful alloying element because it is relatively lightweight. Mo and Nb have the best combination of low density and high melting point.
Niobium (Nb)
Niobium is an element used in superalloys. Nb-based alloys are also used in aerospace engineering as materials for thruster nozzles in liquid rockets.
Iridium (Ir)
There are spark plugs based on iridium that are used in aviation. It is mostly used in electronics-related applications.
Ruthenium (Ru)
When it comes to high-temperature applications, ruthenium is used as an alloying addition to superalloys. Ruthenium may also be alloyed with platinum to increase platinum’s wear resistance, without losing platinum’s other properties.
Hafnium (Hf)
Like many other materials on this list, hafnium is primarily used to alloy with other metals like Fe, Ti, Nb, Ta, and others. C103 alloy, consisting of Nb (89%), Hf (10%) and Ti (1%), was used in liquid rocket thruster nozzles of Apollo Lunar Modules main engine. Sometimes it is added to nickel-based superalloys to enhance adherence of protective oxides layers.
Technetium (Tc)
Technetium is radioactive, which kinda limits its applications. However, it can be used for medical radioactive imaging, and it can also be alloyed with steel to improve corrosion resistance. You just need to be sure this steel is in a place where humans can’t get to!
Rhodium (Rh)
Rhodium is a noble metal that rarely reacts with other chemicals, which can make it a good catalyst. Like Pt, Rh is used for wires that may be exposed to a hot/corrosive environment. Pt can survive high temperatures and corrosion without alloying, which lets it preserve its electrical conductivity. Rhodium is even rarer than platinum.
Vanadium (V)
Vanadium is used in jet engines as an alloying addition to engineering titanium alloy (Ti-6Al-4V). One vanadium-based alloy (V-4Cr-4Ti) is a promising candidate to be used in future fusion reactors
Chromium (Cr)
While chromium has a high melting temperature, it is more known for its low density and oxidation resistance. Cr is the main alloying element (besides iron) in stainless steel, and it is alloyed in superalloy turbines. Even if high temperature alloys don’t directly contain Cr, they may have a thin coating of Cr-alloy for oxidation resistance.
Zirconium (Zr)
When it comes to high temperature applications, zirconium is widely used in the form of zirconium oxide. YSZ – ZrO2-8 wt% Y2O3 (so-called Yttria-Stabilized Zirconia) is a commonly used protective coating which aim is to increase maximum operating temperature of superalloys used in jet engines.
Titanium (Ti)
Titanium is used in compressors of jet engines (Ti-6Al-4V).
Final Thoughts
There you have it! All the refractory metals, including the strict definition of W, Re, Ta, Mo, and Nb; as well as broader definitions that include Ir, Os, Hf, Rh, Ru, Zr, Tc, Cr, V, and Ti.
These metals have high hardness, high melting points, high density, high wear resistance, good corrosion resistance, and poor oxidation resistance. (Not all of these generalizations are true for all metals on the list, especially those that are not part of the main 5 refractory metals).
Refractory alloys are commonly used in high temperature applications, such as welding electrodes, heating coils, rocket parts, and gas turbine blades. Tungsten is the most common refractory element because it has the highest melting temperature, solid mechanical properties, and is also one of the more common refractory elements (so it’s cheap).
Refractory Metal | Vickers Hardness (HV) |
Tungsten (W) | 350 |
Rhenium (Re) | 250 |
Tantalum (Ta) | 89 |
Molybdenum (Mo) | 156 |
Niobium (Nb) | 135 |
Titanium (Ti) | 99 |
Vanadium (V) | 64 |
Chromium (Cr) | 108 |
Zirconium (Zr) | 92 |
Ruthenium (Ru) | 234 |
Rhodium (Rh) | 127 |
Hafnium (Hf) | 180 |
Osmium (Os) | 422 |
Iridium (Ir) | 180 |
The main downside to tungsten is that it is very heavy, so other refractory metals may offer less-dense alternatives.
List of Refractory Metals (“conservative definition”) | W, Re, Ta, Mo, Nb |
List of Refractory Metals (“broader definition”) | W, Re, Ta, Mo, Nb, Ir, Os, Hf, Rh, Ru, Zr, Tc, Cr, V, Ti |
Typical Properties | High melting point, density, and wear resistance; good corrosion resistance; poor oxidation resistance; slow diffusion rates |
Melting Point Range (°C) | 1670 (Ti) – 3380 (W) |
Density Range (g/cm3) | 4.5 (Ti) – 22.6 (Os) |
Hardness Range (HV) | 64 (V) – 422 (Os) |
Price Range (USD/lbs) | Varies greatly from 5 for Cr up to 180,000 for Rh* |
Refractory metals also tend to have slow diffusion rates, so they are often added for creep resistance in alloys. Diffusion rates are dependant on chemistry so there is not a simple rule for which element is the slowest diffuser–but rhenium is famously slow in nickel-based superalloys and gives rise to the “rhenium effect” of excellent creep resistance in nickel-based superalloys.
References and Further Reading
If you like this article, you might also find this post interesting on metals with high melting points.
If you want to know more about alloys in general, here you’ll find our article on this topic.